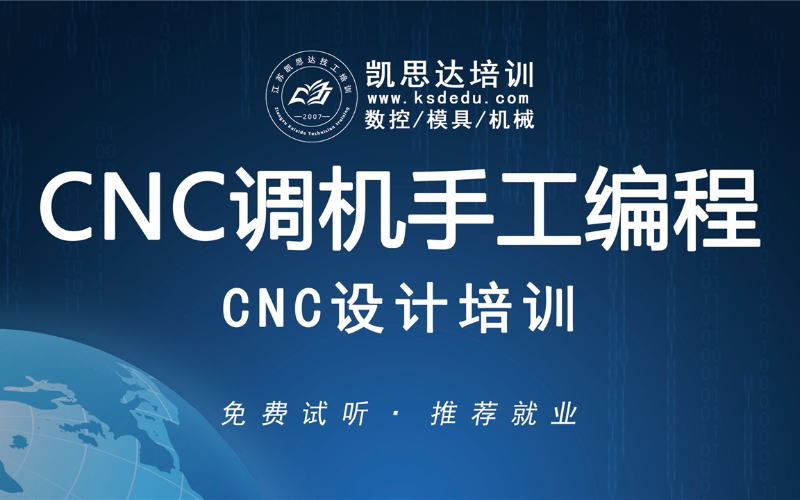


苏州CNC调机手工编程培训班



【课程简介】
参考学时:2-3个月(学不会可免费重学)
学习方式:业余班/周末班/全日班/赴厂内训
学习护航:入学即签订协议
就业支持:就业指导、免费推荐就业
生活支持:提供食宿
实训设施:投资千万、自建实训基地、各型系统齐全
毕业证书:毕业即可考取证书
【招生对象】
工厂普通员工、无经验待业人员、制造业创业人员、机械专业学生、数控爱好者、应届毕业生、转行就业者、数控操机人员、制造业主管、技术加强晋升人员、企业集体内训
【就业方向】
CNC 技术员、CNC 工程师、CNC 数控编程员、CNC 调机员
【教学模式】
从零起点-软件理论-阶段实战-综合实战-免费重修-就业指导
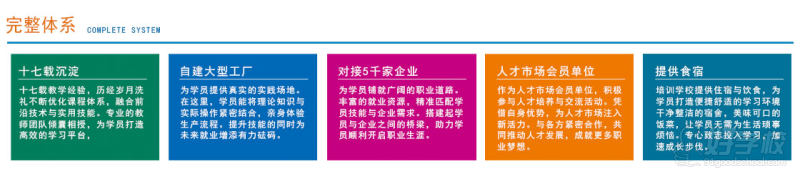
【课程内容】
(一)数控加工基础回顾
1、数控加工原理与机床结构
<1>数控加工的基本原理与工作流程概述
<2>常见 CNC 机床(数控车床、加工中心)的结构组成与功能特点
<3>机床坐标轴的定义与运动方式(直线轴、旋转轴)
<4>机床的主要技术参数及其对加工的影响
2、数控系统概述
<1>主流数控系统(如 FANUC、SIEMENS、三菱等)的介绍与对比
<2>数控系统的操作面板布局与基本功能键的使用
<3>数控系统的显示界面与信息解读(如坐标显示、程序显示、报警信息等)
(二)CNC 手工编程基础
1、编程坐标系与刀具补偿
<1>机床坐标系、工件坐标系的建立与设定方法
<2>刀具补偿的概念、类型(刀具半径补偿、刀具长度补偿)及其在编程中的应用
<3>刀具补偿参数的计算与设置实例
2、基本编程指令
<1>快速定位指令(G00)与直线插补指令(G01)
<2>圆弧插补指令(G02、G03)及其编程格式与应用场景
<3>暂停指令(G04)、程序段跳过指令(G31)等辅助指令
<4>单一固定循环指令(如 G90、G92、G94)在数控车削与铣削中的应用
3、编程实例练习
<1>简单轴类零件的数控车削编程练习,包括外圆、台阶、沟槽等特征的加工编程
<2>平面轮廓铣削的编程案例,如矩形、圆形等简单形状的铣削程序编制
<3>教师指导学员编写程序,并在模拟软件上进行验证与调试,分析错误原因并修改
(三)CNC 加工工艺
1、零件工艺分析
<1>零件图的工艺性审查要点(尺寸精度、形状精度、表面粗糙度要求等)
<2>加工工艺路线的拟定原则与方法(粗加工、半精加工、精加工的顺序与策略)
<3>定位基准的选择与装夹方式的确定(考虑零件的形状、尺寸与加工要求)
2、刀具与切削参数选择
<1>CNC 加工常用刀具的种类、特点与适用范围(车刀、铣刀、钻头、丝锥等)
<2>刀具材料的性能与选择依据(高速钢、硬质合金、涂层刀具等)
<3>切削参数(切削速度、进给量、切削深度)的选择原则与计算方法
<4>刀具寿命与切削参数的关系及优化策略
3、工艺案例讲解
<1>分析典型零件(如轴套类、板类、箱体类)的加工工艺方案,包括工序划分、刀具路径规划、切削参数设定等
(四)CNC 调机操作
1、机床操作基础训练
<1>开机、关机与回零操作的规范与要点
<2>手动模式下的坐标轴移动操作(JOG 模式)与主轴控制
<3>手轮操作技巧与应用场景(精确对刀、微调刀具位置等)
2、对刀操作与刀具数据设置
<1>试切对刀方法与技巧(数控车床与加工中心的不同对刀方式)
<2>对刀仪的使用方法与对刀数据的传输
<3>刀具长度补偿与半径补偿数据的设置与验证
3、程序输入与调试
<1>手工编写程序的输入方法(MDI 输入、程序编辑界面输入)
<2>程序的校验与调试技巧(语法检查、图形模拟、空运行等)
<3>加工过程中的程序暂停、单段执行与跳段执行操作
4、自动加工与监控
<1>自动加工模式的启动与运行监控(坐标显示、切削状态观察等)
<2>加工过程中的常见问题(如刀具磨损、切削振动、机床报警等)及处理方法
(五)复杂零件编程与加工
1、多轴加工编程基础
<1>多轴加工的概念与优势(如四轴、五轴加工)
<2>多轴机床的结构类型与运动学原理简介
<3>多轴加工编程中的坐标系变换与刀具轴控制指令
2、复杂轮廓与曲面编程
<1>非圆曲线轮廓(如椭圆、抛物线等)的编程方法
<2>曲面加工的编程策略(如等高线加工、行切加工、环切加工等)
<3>宏程序在复杂零件编程中的应用实例
3、复杂零件加工实例分析与实践
<1>以航空航天、模具等行业的典型复杂零件为例,进行工艺分析、编程与加工实践
<2>加工过程中的精度控制与质量检测方法(如在线测量、离线检测等)
(六)CNC 加工中的问题解决与优化
1、加工误差分析与控制
<1>尺寸误差、形状误差与表面粗糙度超差的原因分析
<2>从编程、刀具、工艺、机床等方面提出误差控制措施与改进方法
2、机床故障诊断与排除
<1>常见机床电气故障(如系统报警、电机故障、传感器故障等)的诊断方法
<2>机械故障(如导轨润滑不良、丝杠间隙过大、主轴精度下降等)的排查与修复
<3>故障排除后的机床精度恢复与调试
3、加工效率提升策略
<1>优化编程代码以减少空行程与切削时间
<2>合理选择刀具与切削参数提高加工效率
<3>采用多任务并行加工与自动化上下料等技术的应用探讨
(七)综合实训与考核
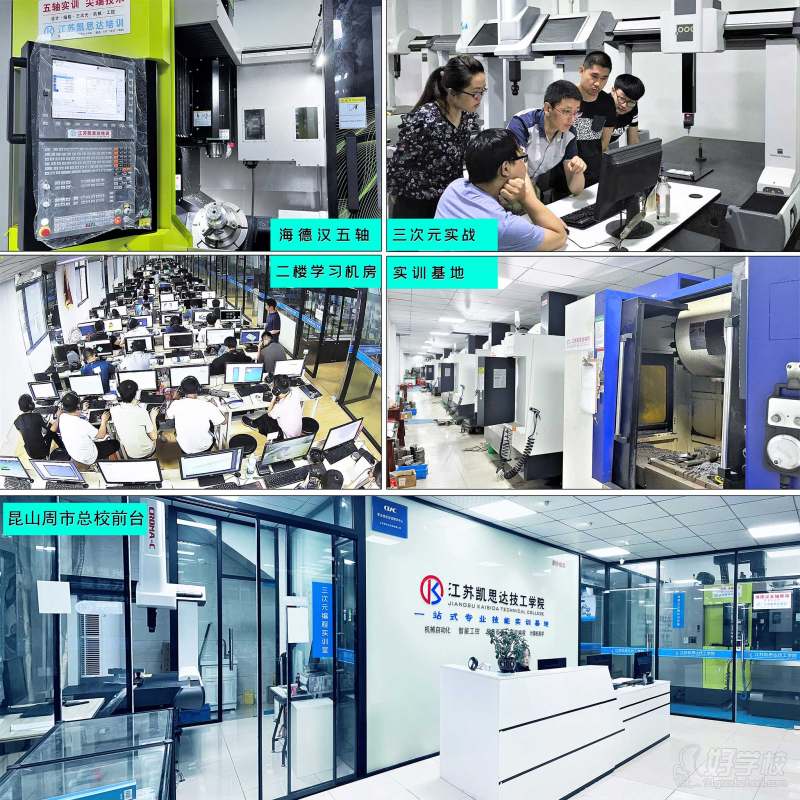
学校环境
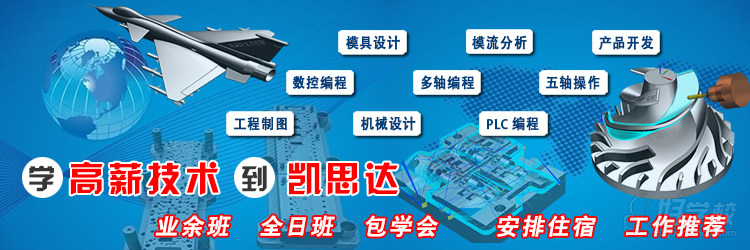
公司介绍
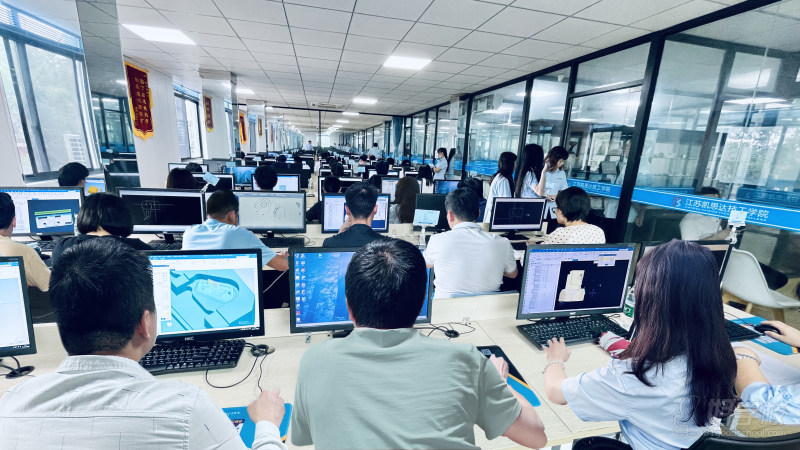

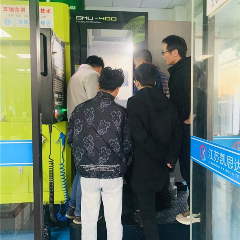
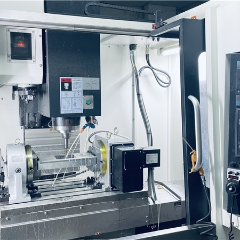
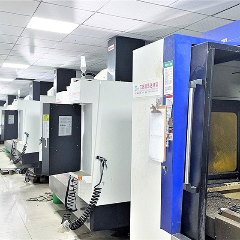
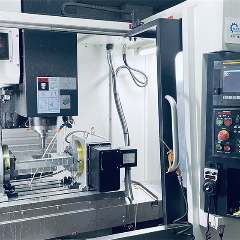

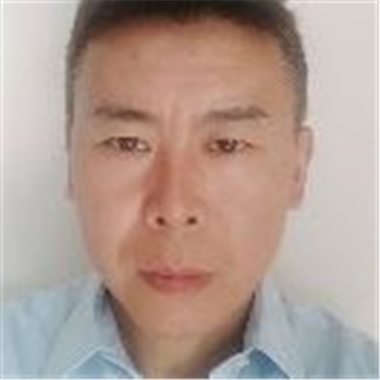

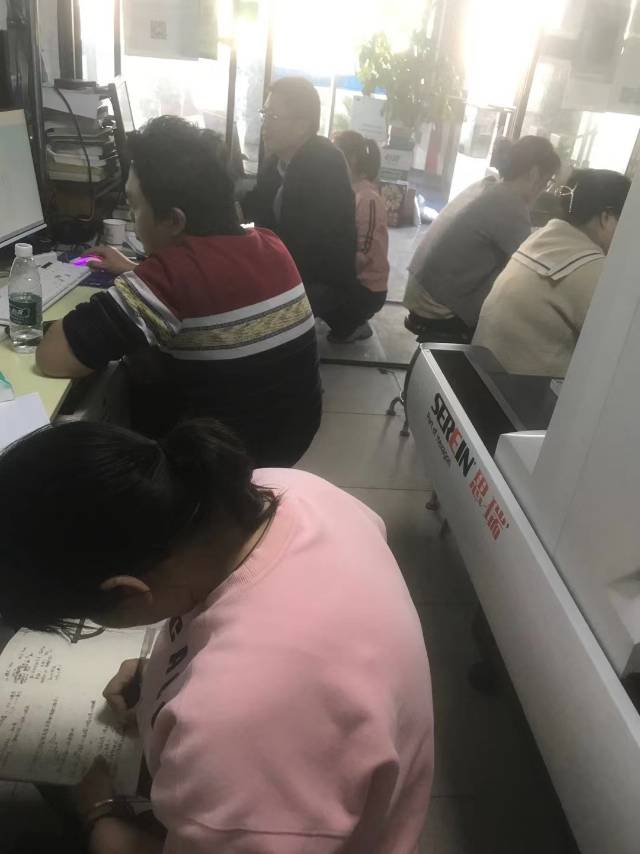
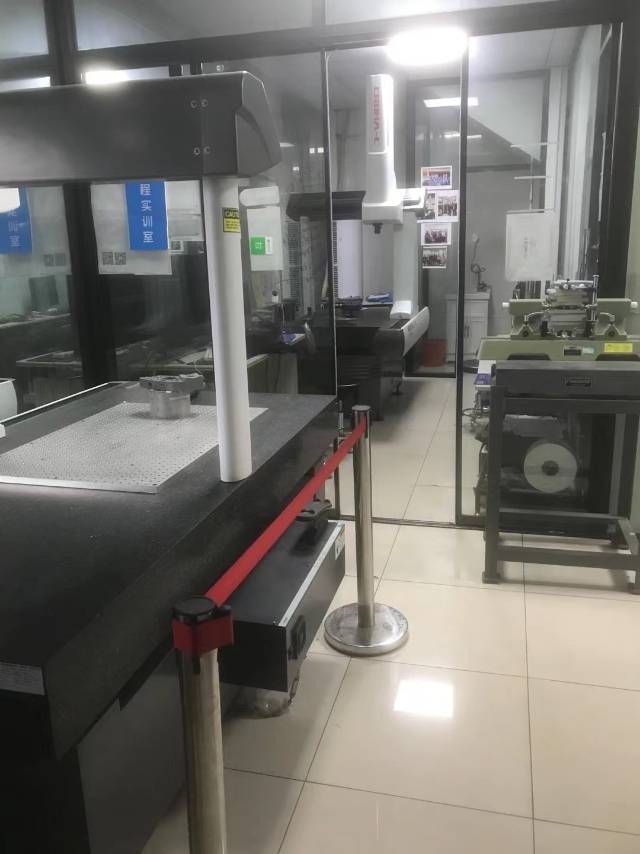
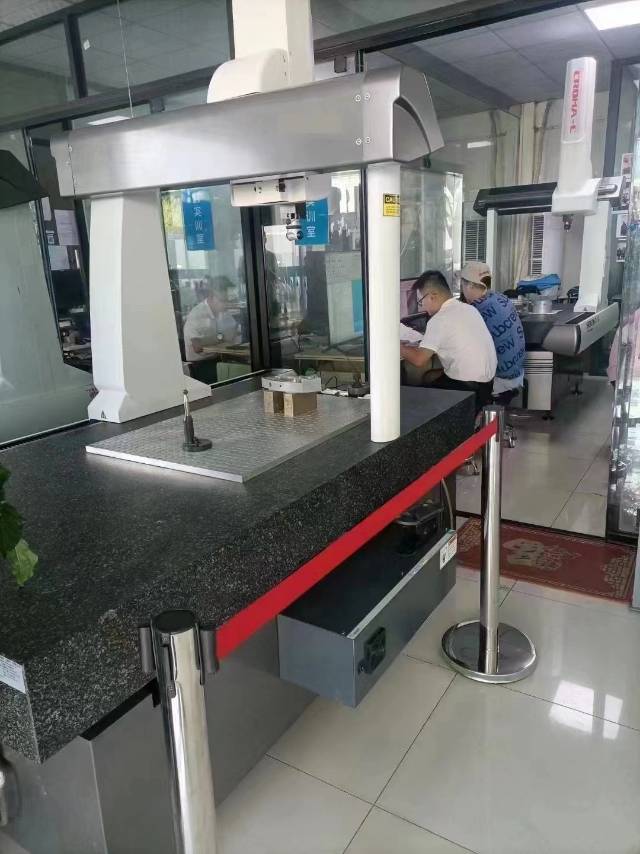
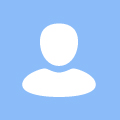

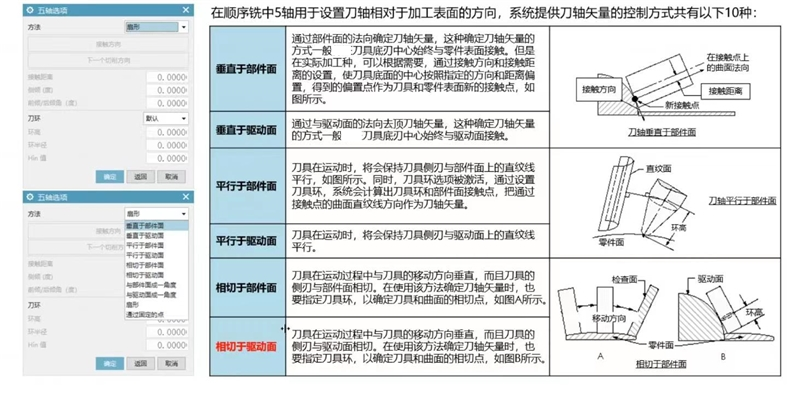
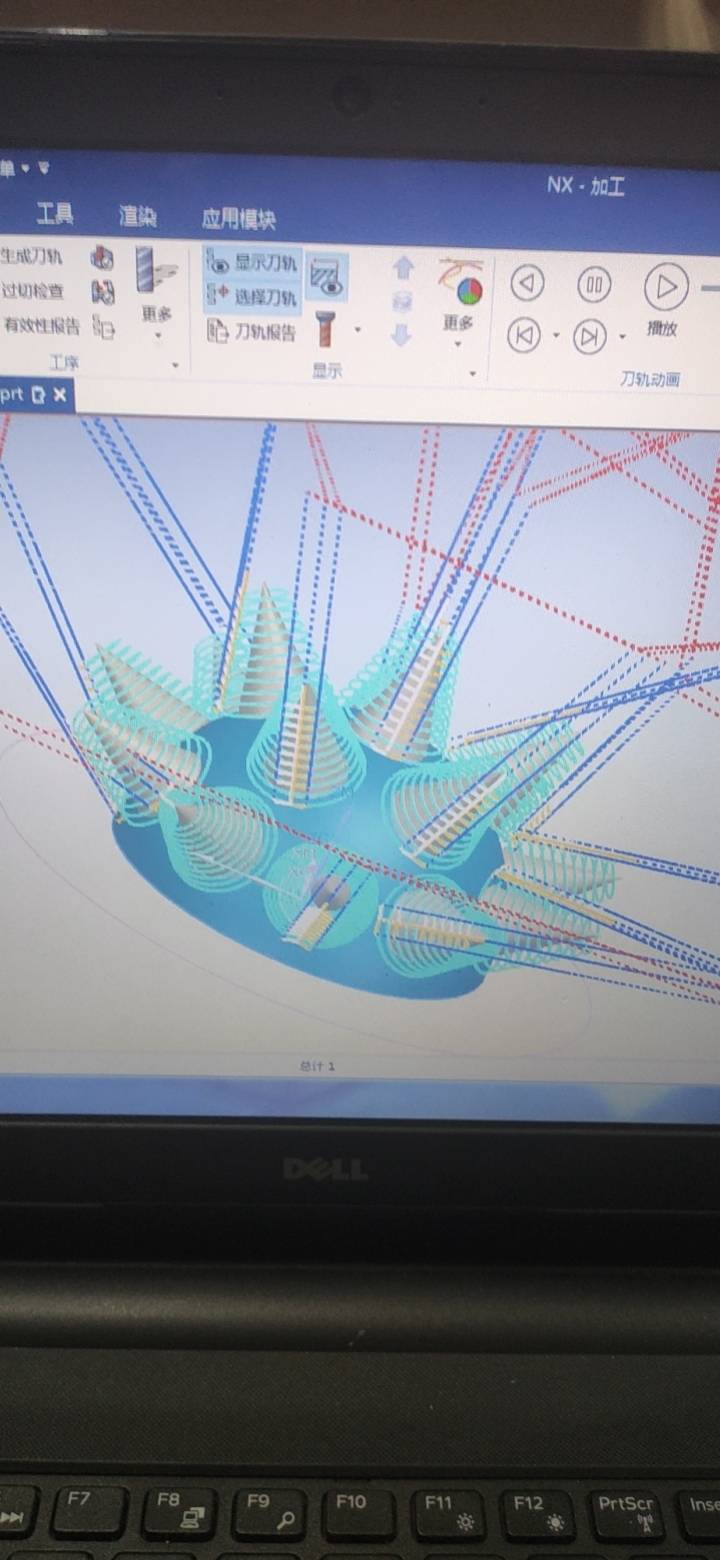
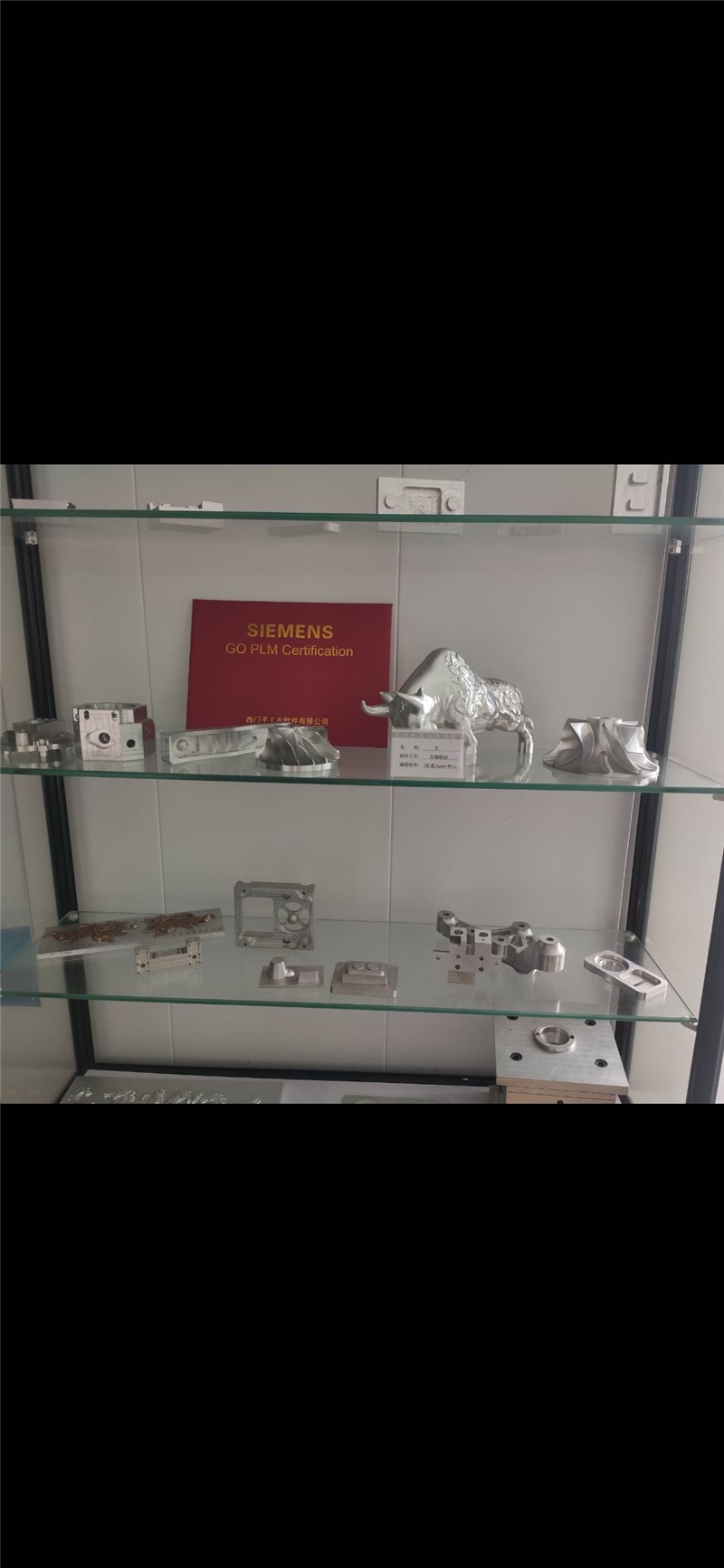
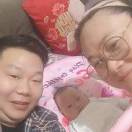

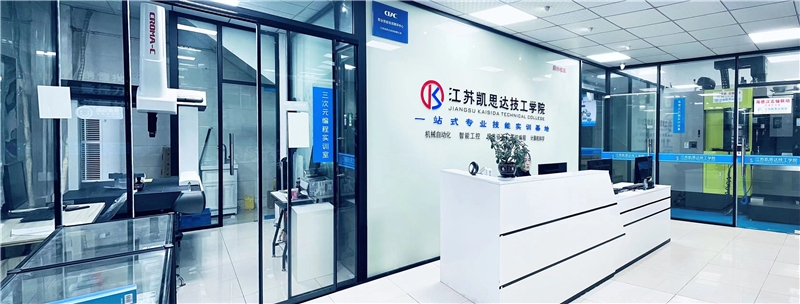
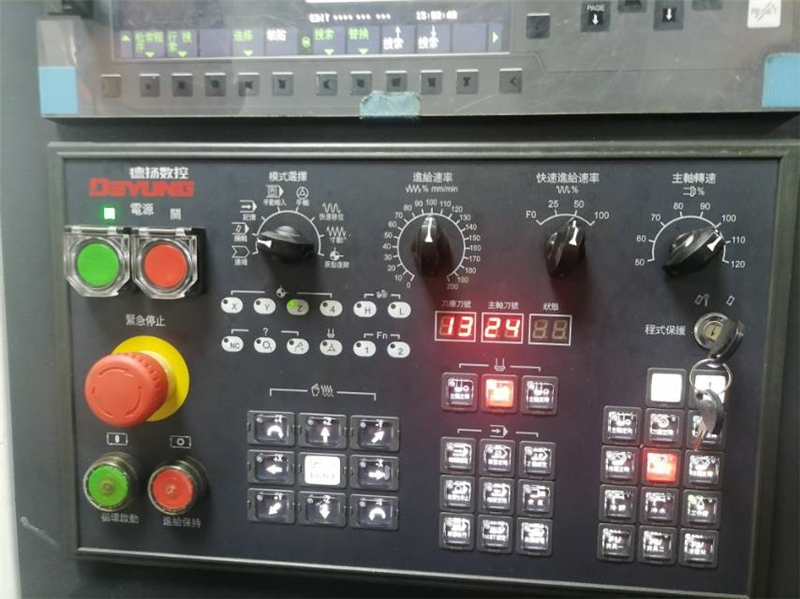
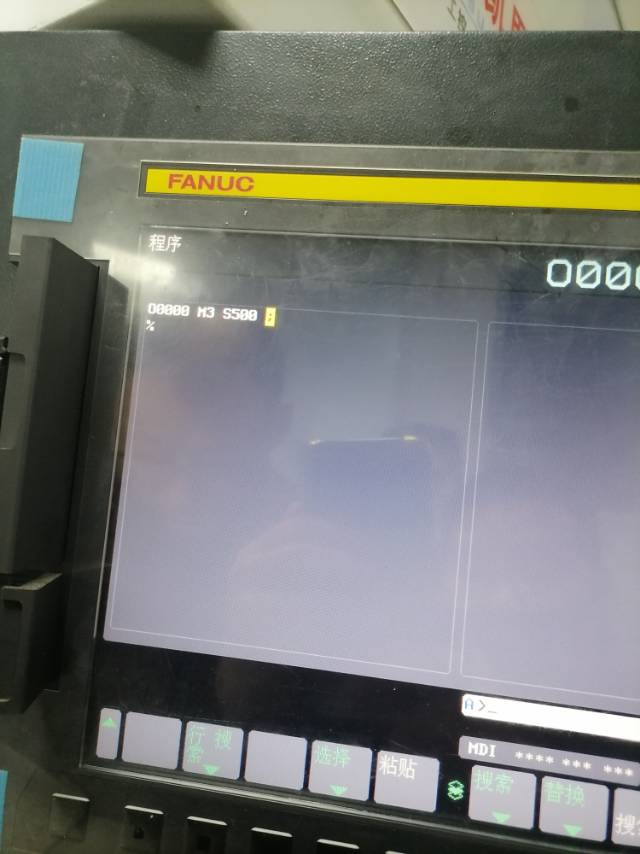